Pharmaceutical Industry
Facing pressure from low-cost competitors, this capsule-maker needed a state-of-the-art solution to let it master the manufacturing basics: product quality, equipment uptime, and wasteful processes.
A manufacturer of pharmaceutical gelatin capsules rose to the top of the industry with its innovative, game-changing products. Its manufacturing processes, however, had remained well behind the curve. As low-cost competitors began threatening market share, the company had to update to a modern system to track quality and efficiency all through its operations in order to maintain its hold on the industry.
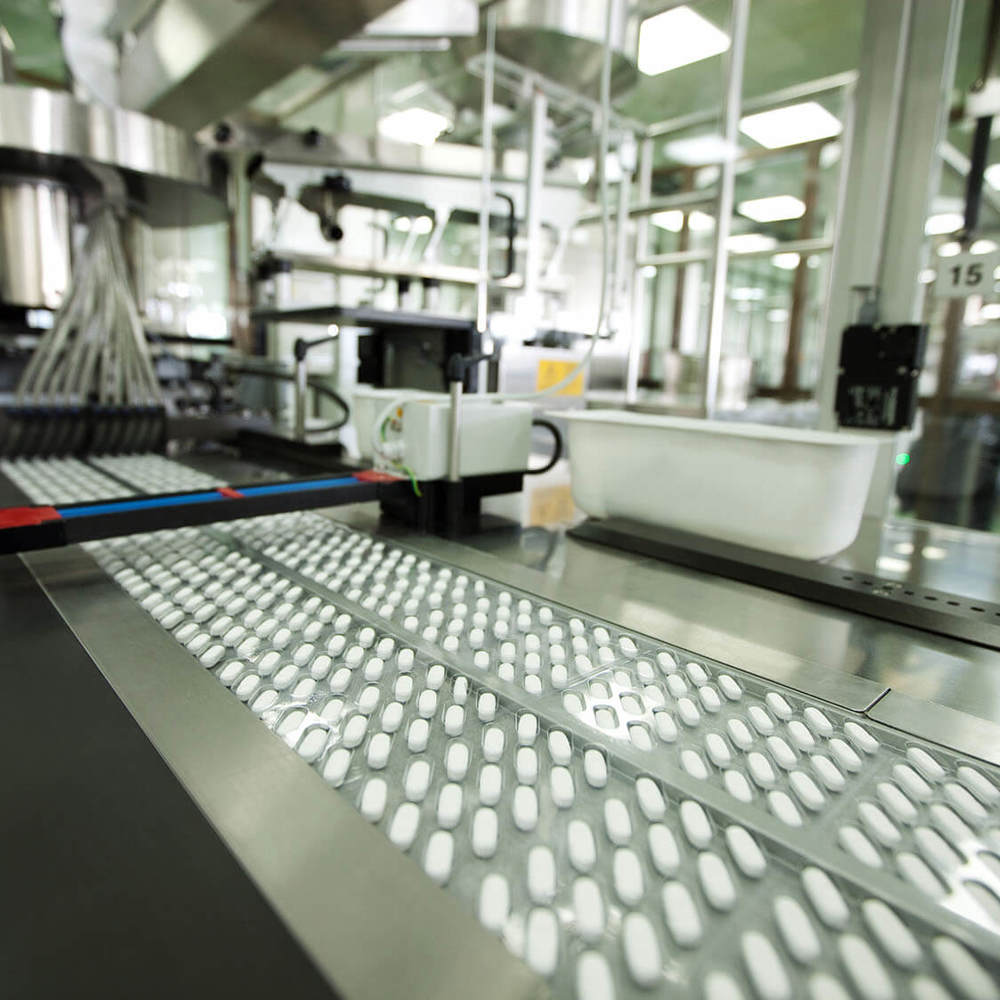
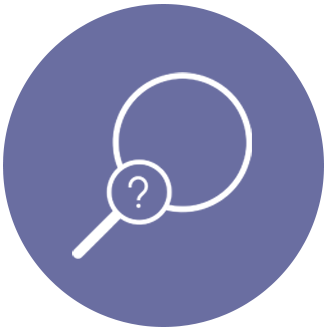
The Problem
In its facility, this capsule maker runs over 60 manufacturing lines, which produce more than 50,000 distinct SKUs, each of which carry unique quality specifications. However, much of the company's quality tracking was still handled through paper records. This was a difficult process that made quick identification of quality issues—let alone correlation of those issues with root causes—nearly impossible.
To stay ahead of the competition, the facility required a comprehensive solution that would enable it to track quality for all of its products in real time, while also providing it with the capability to perform root cause analysis on any issue the system revealed.
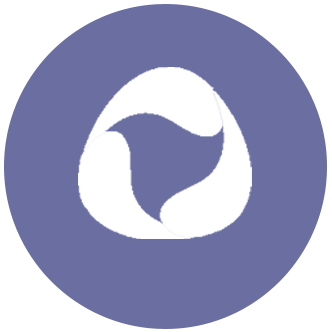
Our Role
Prior to this project, the capsule maker had already partially completed a pilot installation of the GE Proficy platform. RoviSys, a GE Digital partner, carried extensive experience using the system to design quality tracking and genealogy, real-time inventory management, and asset efficiency projects for the life science industry.
This, plus 25 years of experience designing, implementing, and commissioning process control and automation solutions for the pharmaceutical industry, made RoviSys the clear choice to provide this solution.
25 years of experience designing, implementing, and commissioning process control and automation solutions for the pharmaceutical industry made RoviSys the clear choice to provide this solution.

The Solution
RoviSys began by standardizing and synchronizing the controls layer of the company's existing system, which allowed the MES layer to access all production triggers, counts, and downtime inputs.
Once complete, RoviSys then expanded that core solution by implementing standard modules and through a series of custom applications that communicated with the MES. These included:
- A custom product specification management application that allowed templates to be created that could be applied to each of the 50,000 distinct SKUs, which eased the configuration of products and their associated specifications.
- Custom mobile applications designed to run on handheld smart barcode scanners that allowed entry of quality checks.
- A custom application that acted as a middleware layer between the company's automated storage and retrieval system (ASRS) and GE Proficy platform, as well as a simulator that allowed the ASRS controls layer to be simulated, ensuring the ASRS tracking logic was sound.
- A variety of reports and dashboards accessible to quality users, process leads, shop floor operators, and others.
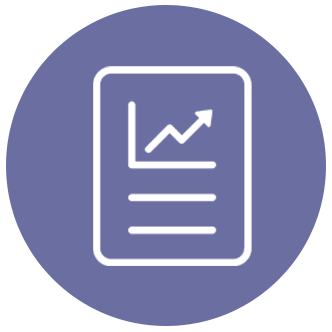
The Results
Point for point, this comprehensive solution allowed the capsule maker to meet all of its critical needs—it substantially reduced quality defects, it allowed for better identification of production issues, and reduced scrap/waste across the facility. In some cases, these results improved quality and operating effectiveness as much as 15% while reducing the effort to run root cause analysis by up to 45%.
In the process, the site's newly integrated ASRS solution led to a 10% jump in customer order fulfillment.
Together, these improvements were enough to resolve the company's fundamental issues: it now has the ability to fully track quality, quickly identify defects, and to pinpoint defect causes in the robust, real-time manner the industry demands. Also, by providing direct insight into the status of machines and equipment—from downtime to maintenance schedules—the solution boosted the manufacturer's efficiency and productivity to levels befitting its innovative product design.
As a result, the capsule manufacturer was not only able to maintain its market position in the face of stiff competition, but also to invest in a facility expansion that will maintain that market hold well into the future.