Taking Clean Rooms To The Next Level
Modular cleanroom manufacturer QleanAir Scandinavia (QAS) is out to disrupt the market, delivering fully traceable, automated condition monitoring in every installation around the world. But to achieve this goal, it first required an all-new remote access system purpose-built to meet rigid quality standards wherever and however they are used.
By carefully regulating environmental conditions—including air quality, temperature, humidity, and pressure—cleanrooms are vital installations in many manufacturing, laboratory, and storage settings to keep workers and samples safe. This Scandinavia-based air cleaner manufacturer is reinventing the market, designing modular, adaptable constructions that meet tight clean room standards while significantly streamlining the installation process.
The next crucial step for the company is to also disrupt the data and control management space by implementing a system that allows users to monitor, track, and adjust conditions easily from anywhere in the world.
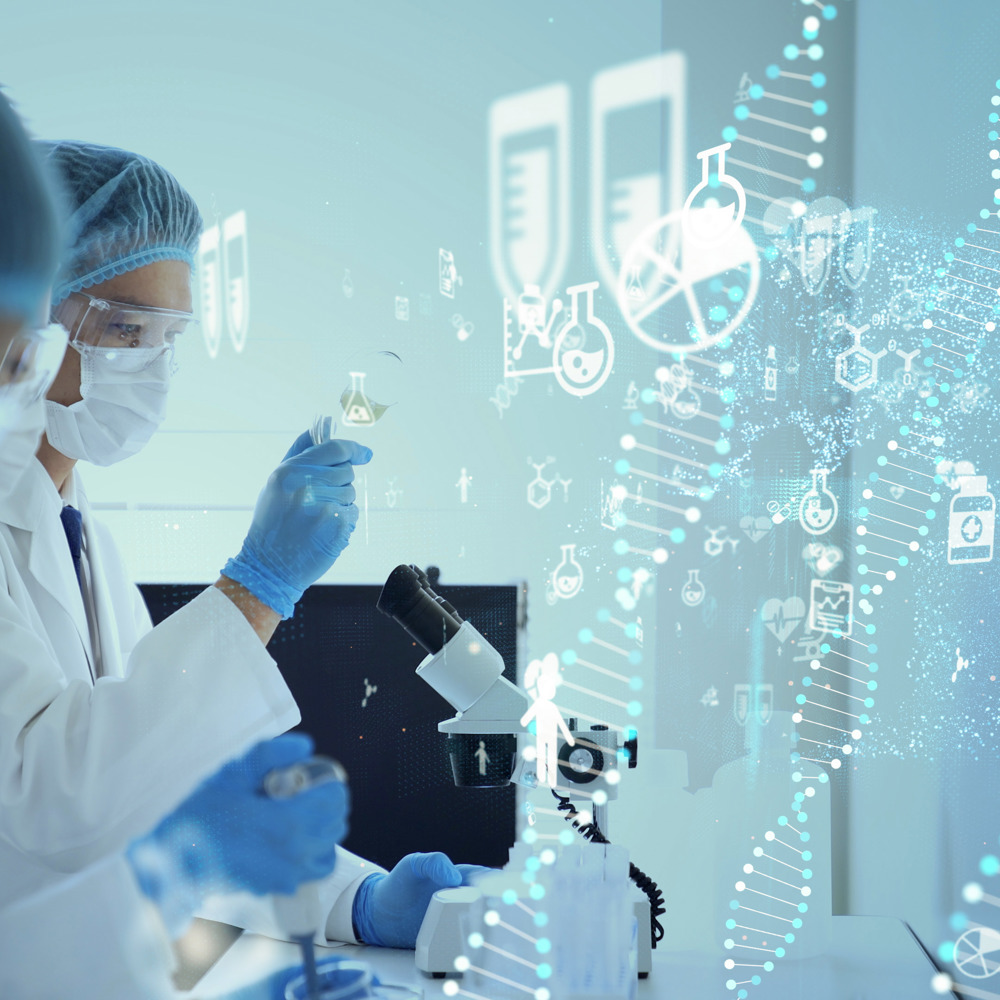
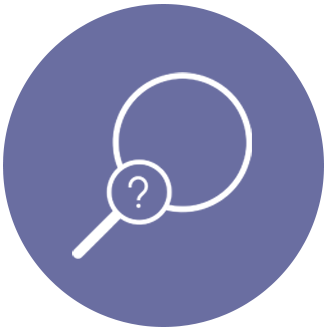
The Problem
To meet quality control standards, clean rooms are required to precisely control the quantity and size of particles circulating in the environment, plus maintain consistent temperature, humidity, and room pressure. Traditionally, these installations are equipped with standard environmental monitoring systems to record critical conditions and metrics in the rooms. This cleanroom maker, however, wanted to take this to the next level.
In order to improve the performance of its products and lower operational costs and maintenance times for its customers, QAS needed an all-new control system that could reliably and consistently track and view both real-time and historical data across the world, automatically and remotely adjust room settings to maintain perfect conditions, and troubleshoot issues virtually through a remote interface.
To achieve such a step-function leap in monitoring and control capabilities, the manufacturer needed a partner with deep understanding of both the technical components of the innovation and of the tight requirements of this industry.
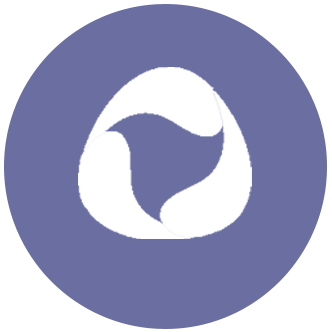
Our Role
RoviSys is a recognized leader in the automation and information space, possessing broad expertise in all the technical requirements of this project—from data collection and instrumentation to communication and controls. But the company also carries decades of experience and expertise specifically in the life science industry, with a long record of success specifying, designing, and commissioning cleanrooms and lab spaces in the pharmaceutical manufacturing environments.
Combined, these assets made RoviSys the only contender capable of delivering exactly what the company needs.
This private-cloud setup provides cleanroom owners, operators, and technicians immediate and secure access to both real-time and historical data on room conditions.

The Solution
RoviSys began by designing a new monitoring system for QAS modular cleanrooms, which included an array of off-the-shelf building automation controls and instrumentation selected to provide exactly the visibility and remote access the project required. Next, it provided on-premise, cloud-connected controllers for the system. This private-cloud setup provides cleanroom owners, operators, and technicians immediate and secure access to both real-time and historical data on room conditions. Primary solutions included Tridium Niagara 4 interface and AWS cloud infrastructure.
RoviSys was then able to integrate these installations, allowing users to control each bank of supply fans in each room using the same interface. This critical step provides the capability to monitor, control and support conditions remotely no matter where the cleanrooms or its operators are located. Built-in alarming functions enhance the effect of this capability, alerting both the end user and the manufacturer of any out-of-spec fluctuations within 5 seconds.
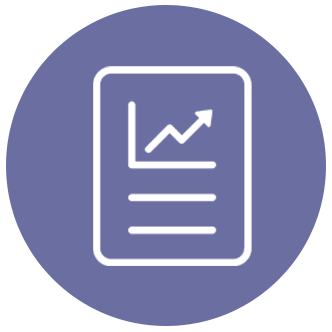
The Result
With these automation, control, and instrumentation solutions in place, QAS successfully achieved its core mission: to further innovate the clean room space by delivering remote capabilities to its core product.
By doing so, it was able to increase both the reliability and uptime of its cleanrooms while also reducing time and costs for operation and maintenance. In the process, the company recorded a notable increase in customer satisfaction everywhere the new systems are deployed.