Refining the Ingredients for Automation Success
To reap the full benefits of Industry 4.0 technologies, this global supplier of agricultural commodities needed to overhaul the outdated control infrastructure at one of its U.S. facilities. With this initiative, the company also aimed to develop a template that could be replicated at its other sites throughout North America.
A vital link in the producer-to-consumer food chain since the early 1900s, this company has continuously grown and evolved by focusing on innovation and consumer food trends, while adding capabilities such as value-added processing, refining and milling.
At one of its facilities in Illinois, the company has shifted from producing chicken feed to refining soybean oils for in-demand food products and healthier frying oils. While the refinery makes food products that are on the leading edge of consumer preferences, its decades-old control system was a throwback to an earlier time – and a drag on operational efficiency. In a highly competitive market, the company saw an opportunity to bolster its competitiveness by modernizing its control backbone.
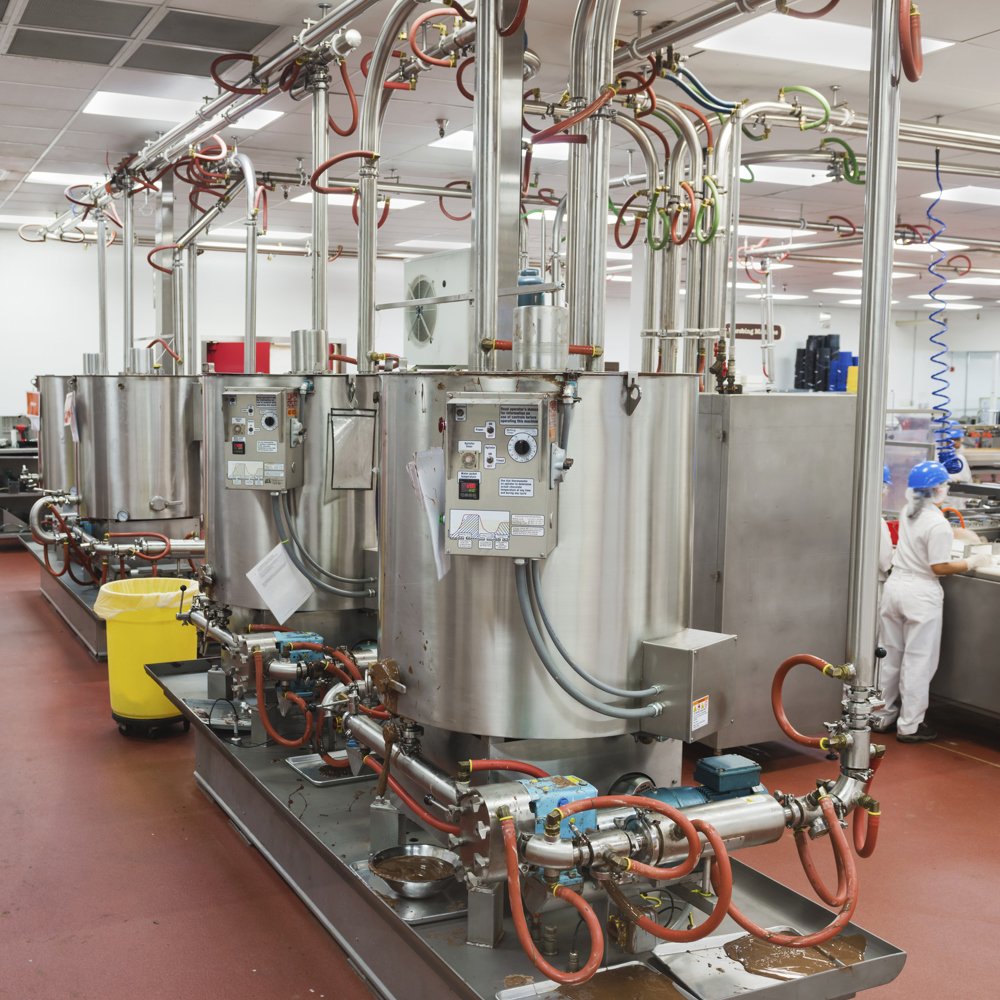
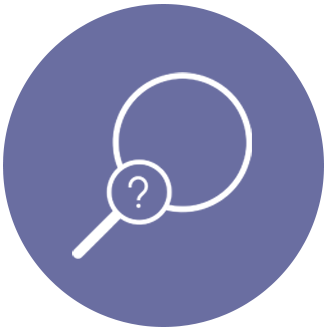
The Problem
The Illinois facility is a complex operation. The site is engineered to run multiple product recipes simultaneously, and to quickly change-over production lines to flex with demand.
The control system, however, no longer supported the facility’s production goals. The control hardware was approaching obsolescence, the operational data was unreliable and the system’s reporting and analytics weren’t robust enough to provide meaningful, actionable insights that drove operational improvements. Additionally, operators and users were struggling with the system alarms and interfaces. Maintaining the system had become an onerous task, as replacement parts were hard to find – and expensive when they were available.
The company determined that the best course of action was a full replacement of the control system. A successful implementation was critical, as the company aimed to adapt a similar model at its other North American locations as part of a ten year digital transformation initiative.
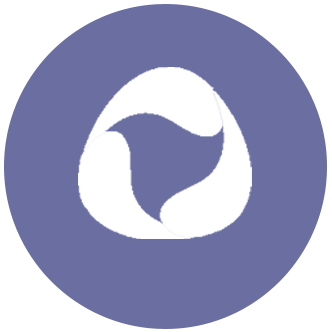
Our Role
This project was in the proverbial “sweet spot” for RoviSys, which brought more than three decades of experience delivering leading-edge control solutions in food & beverage facilities and batch-production environments.
The customer had selected Rockwell Automation hardware and software for its new control platform. As a Rockwell Automation Platinum System Integrator Partner – the highest level of partnership within the Rockwell program, RoviSys was ideally suited to implement the Rockwell solution in support of the customer’s digital transformation.
The customer established a nine-month timeline for the project. Commissioning was slated to coincide with the facility’s annual two-week maintenance shutdown. RoviSys dedicated six full-time engineers to bring this project to a successful conclusion.
The end result has exceeded expectations. Since the installation of the new control system, production output has doubled. The client had hoped to recoup its investment in six months, but has realized a positive ROI within the first three.

The Solution
The RoviSys team methodically tackled the task at hand by identifying the project scope, goals and benchmarks as well as the system requirements and risks. The team drafted functional specifications and offered system recommendations. Their recommendations included utilizing FactoryTalk Historian to obtain real-time process and production information, and leveraging FactoryTalk Batch to reduce the complexity of recipe management and increase the flexibility of recipe formulations.
Finalizing the project parameters and details was a collaborative effort between RoviSys and the customer’s leadership and operations teams. When the customer approved the final plans, coding and implementation began in earnest. RoviSys conducted factory acceptance testing of the new control system at its engineering office in Aurora, Ohio.
RoviSys engineers worked around the clock during the two-week installation phase. Keeping existing wiring in place, the RoviSys team removed old Honeywell controllers and installed eight new Allen-Bradley ControlLogix controllers. Thorough recipe and phase testing ensured that facility would hit the ground running when the new system went live.
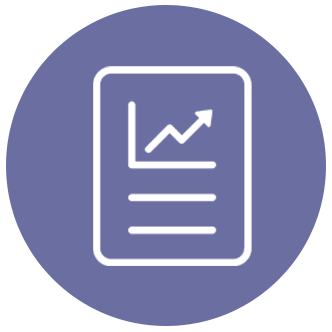
The Result
For this complex project, RoviSys delivered a successful implementation and a seamless startup on time and on budget.
The Rockwell platform has fast-forwarded the facility’s control infrastructure into the Industry 4.0 age. With solutions such as Rockwell’s PlantPAx distributed control system, operators are empowered to make better, faster control decisions thanks to reliable embedded alarms, high-performance graphics, SAMA diagrams, highly integrated HART and other technical features.
The end result has exceeded the customer’s expectations. Since the installation of the new control system, production output has doubled and product quality has improved. While the client had hoped to recoup its investment in six months, the company realized a positive ROI within three months. The smooth execution of the project is serving as a catalyst and a model for similar initiatives at other sites throughout North America.