Inking A Digital Revolution
An industry-leading printer ink manufacturer still relied on manual paper logs to track consumption and movement of over 100 raw materials. To maximize efficiency and reduce human error, the plant needed a digital makeover.
Printer ink manufacturing is a complicated business. Producing the consistent, vibrant colors consumers demand requires precise mixing of a complex array of pigments, dyes, dispersants and additives processed in careful recipes where the smallest variation could have a significant impact on the quality of the batch.
In this setting, robust material management is essential. Material shortages, product mix-ups, or delivery delays can spell disaster for both product quality and plant productivity.
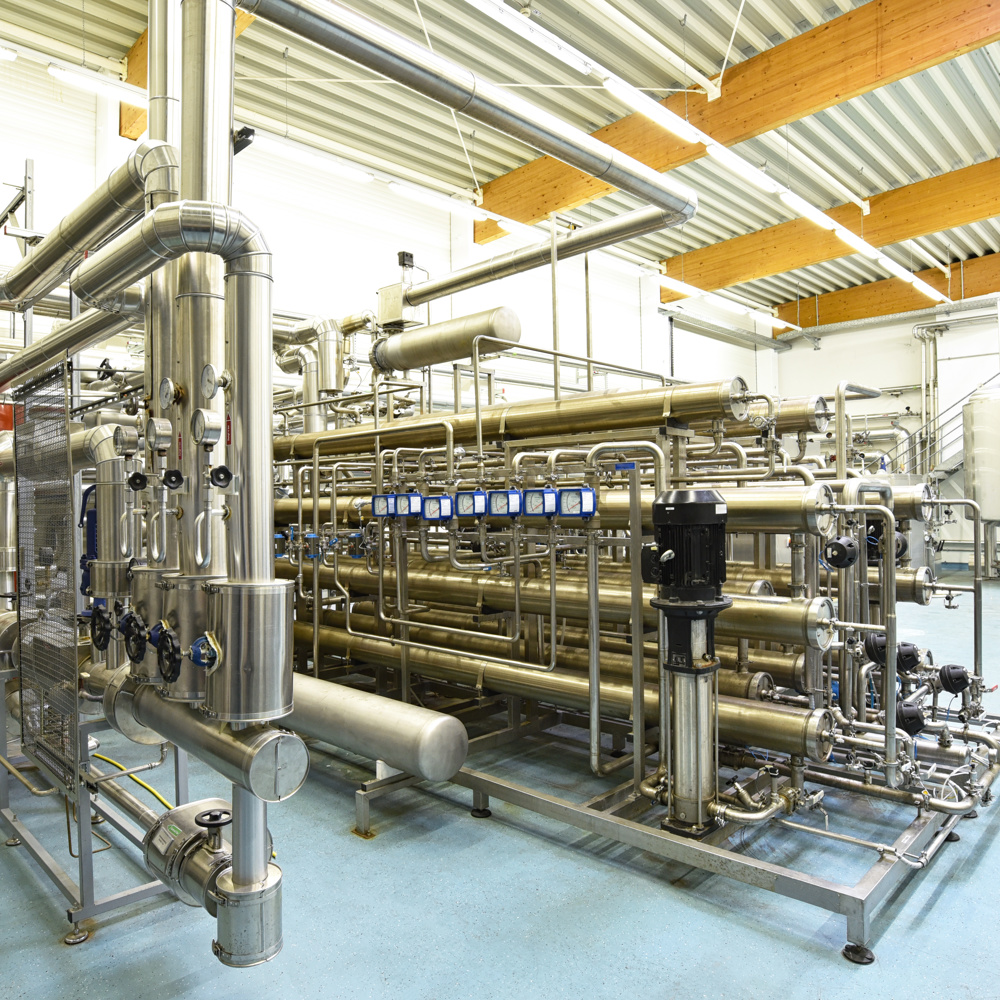
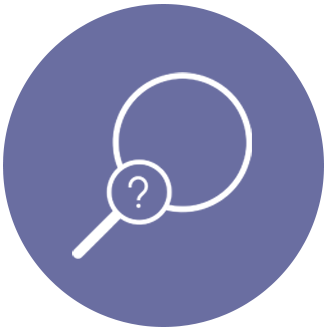
The Problem
This plant located in Singapore, is responsible for producing a wide range of consumer and industrial printer inks used in businesses and homes across the world. The facility mixes and processes dozens of compounds and materials for each of the essential colors it produces, which requires precise tracking and management to maintain production schedules and product quality.
However, the plant had no system in place to automatically track consumption and movement of these critical components, relying instead on paper logs filled out manually after each raw material transfer. This system led to multiple human errors across production and created the potential for serious errors—such as attaching the incorrect raw material to dedicated pumps.
To reduce these errors and enable a way to track the batch quality and its raw material genealogy, the plant needed a digital transformation of its material management system plus an experienced integrator who understood the complexities of process manufacturing to implement it.
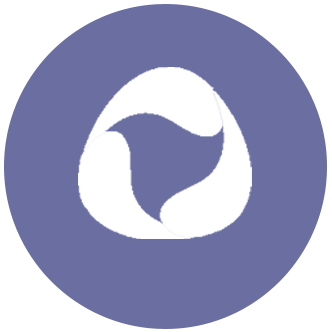
Our Role
To succeed in this transformation, the plant required a host of software, reporting, and digital management systems installed, plus a system that would simplify data entry and reduce human errors. All of which had to work efficiently and effectively in a busy, complex manufacturing setting with hundreds of processes and materials to track.
This meant it needed a system integrator that carried deep experience in controls, reporting, and material management as well as in the real-world complexities of process manufacturing. In this respect, RoviSys was the ideal partner. They could deliver the results required.
The project timeline was very tight. The FTBatch implementation was done in phases within a span of a month and the timeline was met with strong support from the RoviSys team. The team successfully launched FTBatch which helped us to proceed with our first batch runs for different products without any deviation or observation.

The Solution
The first challenge for this project was to cover the obvious software gaps in the legacy system. The previous configuration carried no batch engine and all batch recipes were organized on the PLC layer, which made managing changes difficult. To correct this—and taking into account the plant’s immediate needs and existing architecture—RoviSys selected Rockwell Automation’s FactoryTalk Material Manager and FactoryTalk Batch, which it coupled with an event archiver and SQL server reporting services. Together, this system provided the digital backbone the plant needed to accurately track and manage materials as they moved across the floor.
RoviSys then took on the data entry issue. Here, it replaced paper logs with a barcode scanning solution that is directly integrated to the new material management system. This allowed operators to simply scan in materials used for every batch, thereby removing the risk of errors and adding critical real- time tracking capabilities.
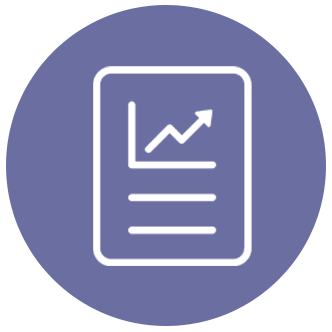
The Result
This new material management system equipped the production team with fully-automated and consolidated platform that can accurately monitor inventory consumption in real time and manage new material introductions to the system. It puts clear and detailed specifications of every raw material log, plus their usage, right at the operators’ fingertips. Along the way, human error in tracking raw material usage and movement was significantly reduced.