Harnessing The Potential of Fault Detection and Diagnostics To Maximize Uptime
Abbott, a global leader in nutrition, research and development, has leveraged plant-floor automation and information systems to transform innovation into life-changing health products. Always focused on improving, the company saw the potential for process analytics to deliver efficiency improvements and cost reductions at its Casa Grande, Arizona, manufacturing facility.
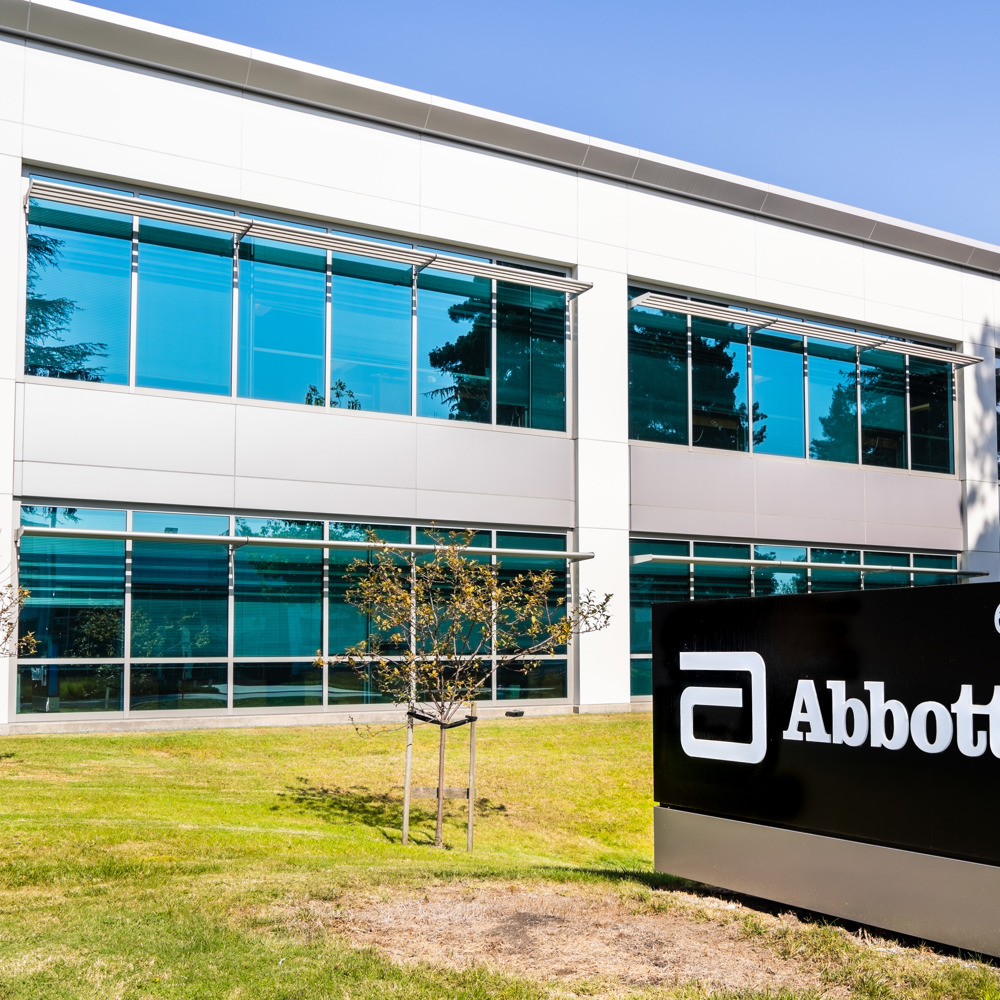
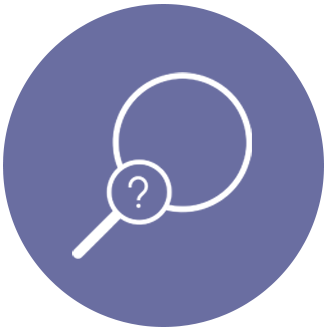
The Problem
For decades, Abbott has used PLCs to control machines, processes and equipment at this facility. The next phase in the evolution of its plant-floor automation was exploring how the information gathered from its control systems could be used to analyze processes and improve operational efficiency. Before Abbott embarked on a plantwide analytics effort, owners needed to identify available data by looking at existing control systems, instrumentation, connectivity and data collection. Additionally, they needed a better understanding of the real value of data available from equipment.
ICONICS, a Massachusetts-based provider of automation-software solutions, approached Abbott about conducting a pilot study to evaluate its Fault Detection and Diagnostics (FDD) technology. Using an advanced algorithm, the FDD software is designed to reduce costs and improve operational efficiency by predicting, reducing and eliminating equipment downtime. Although Abbott already was applying analytics to its repository of process data, the company was intrigued by the FDD technology. RoviSys
Building Technologies (RBT) partnered with ICONICS to make the case for FDD, and Abbott saw enough potential benefits that it decided to move forward with the pilot study.
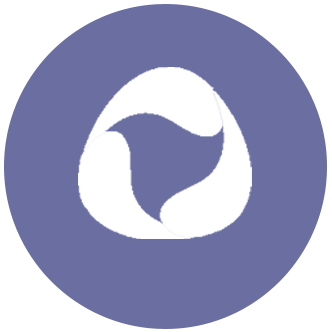
Our Role
The FDD software leverages an advanced fault-rules engine that calculates fault probability as well as all associated costs. In addition to determining the probability that a specific piece of equipment will fail, the technology advises personnel of specific actions they can take to prevent faults from occurring. If a fault occurs, the system displays the cost of the fault and can provide probable causes. The information gathered is used to diagnose problems, prioritize repairs, reduce equipment downtime and lower maintenance costs.
Abbott, RBT and ICONICS collectively identified the energy center at the Casa Grande facility as the area that stood to reap the greatest savings and where FDD could be readily implemented based on available data. As an ICONICS Gold Partner Systems Integrator, RBT brought software-deployment experience, HVAC and mechanical equipment expertise, and a deep understanding of facilities that make nutrition products.
It’s estimated that the Fault Detection and Diagnostics solution has delivered 5% to 10% in savings on annual energy costs.

The Solution
In the initial information-gathering phase, the RBT team reviewed facility drawings and documentation
to better understand the scope and depth of the project. A visit to Casa Grande to meet stakeholders
and tour the facility provided an opportunity to gather information about existing equipment and
system drawings, network diagrams, operating descriptions, existing HMI graphics and existing tag lists.
After gaining a comprehensive understanding of Abbott’s needs and requirements, RBT engineers began
developing the ICONICS system in Microsoft Azure cloud. This included graphical displays, cost
calculations and configuration. The RBT team configured more than 1,600 real-time tags, 600 Hyper
Historian tags, asset classes and fault equations for air handlers, boilers, chillers, air compressors and
cooling towers. RBT also established a site-to-site VPN connection with the Abbott network, allowing
ICONICS to pull real-time data from an OSISoft PI used for data collection. Shortly thereafter, RoviSys
Building Technologies deployed the visual tool to interface with this system, which enables equipment
operators to easily view fault information and energy costs and make determinations about equipment
operation.
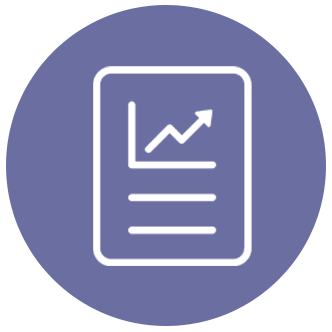
The Result
RoviSys helped Abbott budget for the implementation by analyzing utility bills and establishing a project
scope with a two-year payback based on projections. It’s estimated that the FDD solution has delivered
5% to 10% in savings on annual energy costs. Insights provided by the FDD solution have allowed plant
operators to quickly identify faults, recognize energy inefficiencies and empower maintenance teams to
make informed decisions and prioritize support and repairs.
A fault with a particular air handler illustrates how the FDD software paid immediate dividends in energy
savings. An air-handler fault for “overcooling” was triggered because the unit was supplying air that was
below setpoint for several hours. An operator received a real-time notification from the FDD system.
Upon investigating, the operator discovered that the outside and return air dampers had been removed
and the damper between the return air and supply air had locked closed. The space was being
overcooled because the supply fan had to run at 100% to attempt to meet the pressure setpoint.
However, the setpoint couldn’t be met because the return-air fan was manually exhausting air at 100%
to relieve pressure. The FDD solution prevented the air handler from continuing to consume energy and
waste money. Instead, the operator was able to improve efficiency by rebalancing the system.
Based on the success of the initial implementation, Abbott identified opportunities to apply FDD in other
areas of the Casa Grande plant as well as other Abbott facilities.