Fueling The Semiconductor Industry With Real-Time Intelligence
An equipment maker at the front-line of the semiconductor demand surge harnessed real-time material data to improve consistency and reduce errors.
This U.S. based manufacturer of chemical-mechanical products and equipment that is critical to the production of semiconductors relied on manual raw material data and Excel spreadsheets to track production and batch data. To meet skyrocketing global demand in the industry, it needed to automate data collection across its operations to provide real-time material tracking and management capabilities.
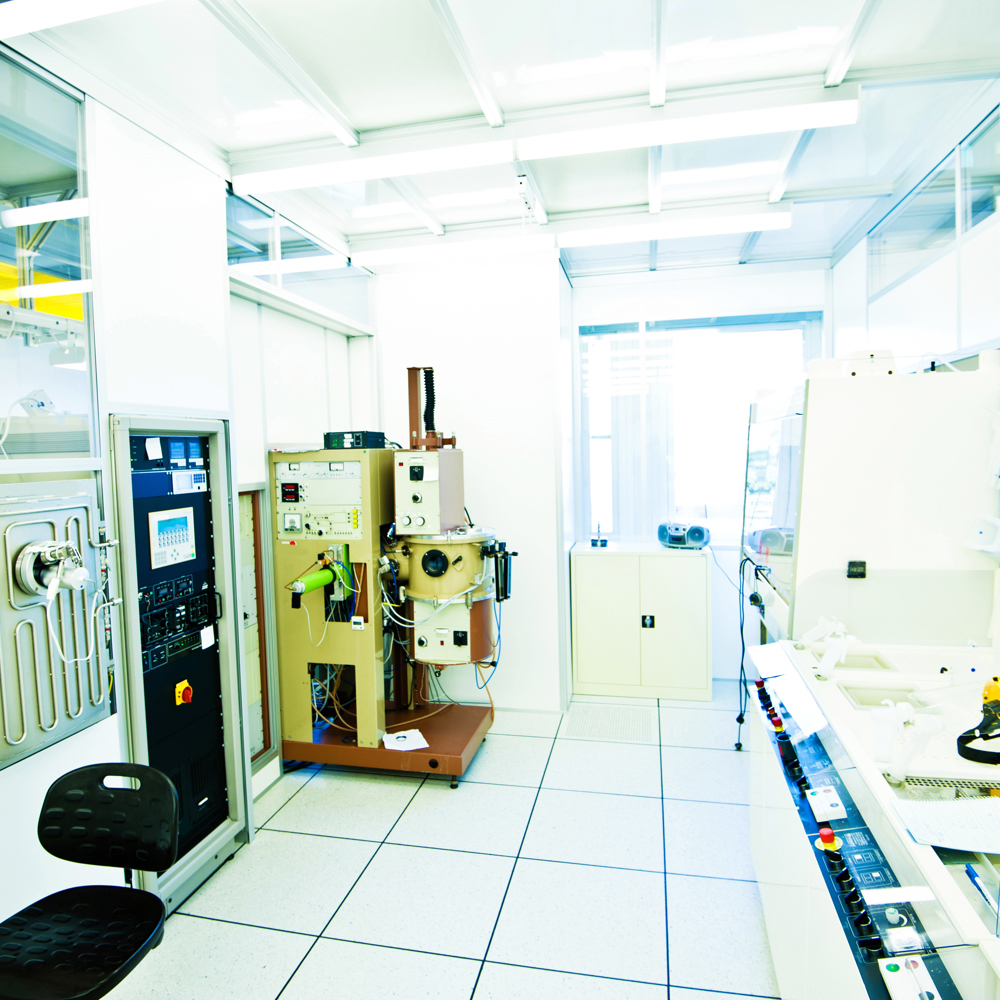
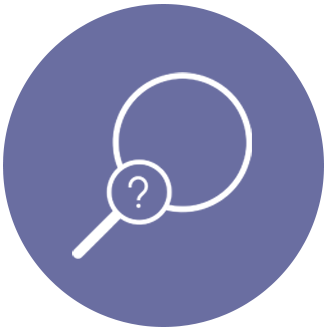
The Problem
The need for semiconductors is at an all-time high, maxing out production in labs around the world as autos, appliances, and products across the consumer market demand more internal computing power.
This manufacturer produces chemical-mechanical equipment that directly enables the production of these semiconductors, putting its product in at the center of one of today’s most critical industries.
The problem is that, while the company had deployed and standardized its production data on a Dell Boomi system, its material management process was still entirely manual. Operators manually input data for each raw material and their various batch specifications into Excel spreadsheets, which was then used to tabulate portions and requirements for all
future calculations.
This was not only a tedious task for operators but the process was also prone to human error and inaccuracies which impacted product quality. Due to the strict requirements of the semiconductor industry, this effectively meant that the rate at which products are being shipped to the customer were also decreased.
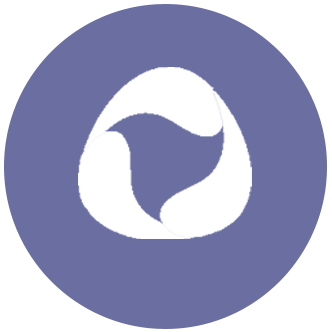
Our Role
To overcome this challenge and meet the growing global demand for its products and equipment, this manufacturer required much more than just an OT integrator. It needed a partner that understood the complexities of batch and process manufacturing, with decades of experience with both data automation and material management, and carried industry-leading expertise in implementing today’s top technological resources needed toaccomplish these goals.
With RoviSys understanding the intricacies of chemical mass balance calculations, as well as deep technical knowledge in utilizing S88 batch control to make their processes as modular as possible, the client reached out to RoviSys to support the execution of this vision, despite RoviSys not being within close proximity of the plant.
This eliminates the tedious and error-prone process of manual data entry and provides access to realtime data across the company’s entire material management system.

The Solution
To resolve this manufacturer’s material data problems, RoviSys tapped its deep well of expertise to design a custom solution that automatically captures and tracks all necessary information and ties that data seamlessly back into the plant’s Dell Boomi and LIM software.
This “Pick List Bespoke Solution” primarily consists of an SQL database that consolidates metadata from FactoryTalk Transaction manager and FTHistorian SQL database, which provides users with the ability to organize the required data directly through a Pick List Web Application’s individual schema tables. This system then connects to the pre-existing infrastructure, allowing it to easily query production data, part numbers, and batch and material information in real-time from a single database.
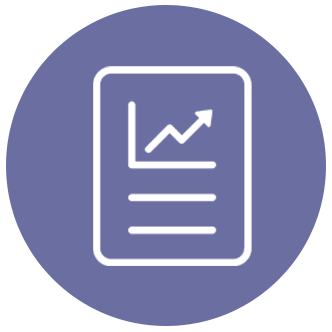
The Result
With this system in place, the company now possesses a powerful material management and tracking system that allows it to automatically calculate and determine the percentage combination of each raw material based on the specifications of each batch, with consumption data immediately routed back to the ERP system.
This eliminates the tedious and error-prone process of manual data entry and provides access to realtime data across the company’s entire material management system.
With this access, the manufacturer was able to develop batch reports that are able to fulfill the semiconductor industry’s increasingly strict data recording requirements.
And this success is only the beginning—based on these results, the manufacturer is working with RoviSys on four new major integration projects to improve and perfect its batch automation and Pick List systems.