Fast Tracking A Vaccine For COVID-19
The year 2020 always will be remembered as the year of the pandemic. As SARS-CoV-2 brought entire economies to a grinding halt – and healthcare systems buckled under the crush of sick patients – an unprecedented response was underway to develop a vaccine. With help from RoviSys, this premier biotech manufacturer quickly ramped up production of a vaccine that held the potential to save millions of lives.
This global leader in pharma planned to repurpose existing manufacturing space at its Michigan facility, as part of the production ramp-up needed to meet COVID-19 vaccine demand regionally and globally.
Working on an accelerated timeline, the goal was to expand production space from 3,000 to 30,000 square feet and while simultaneously integrating brand-new processing equipment. The scope and fluid nature of the project required a partnership with a master systems integrator.
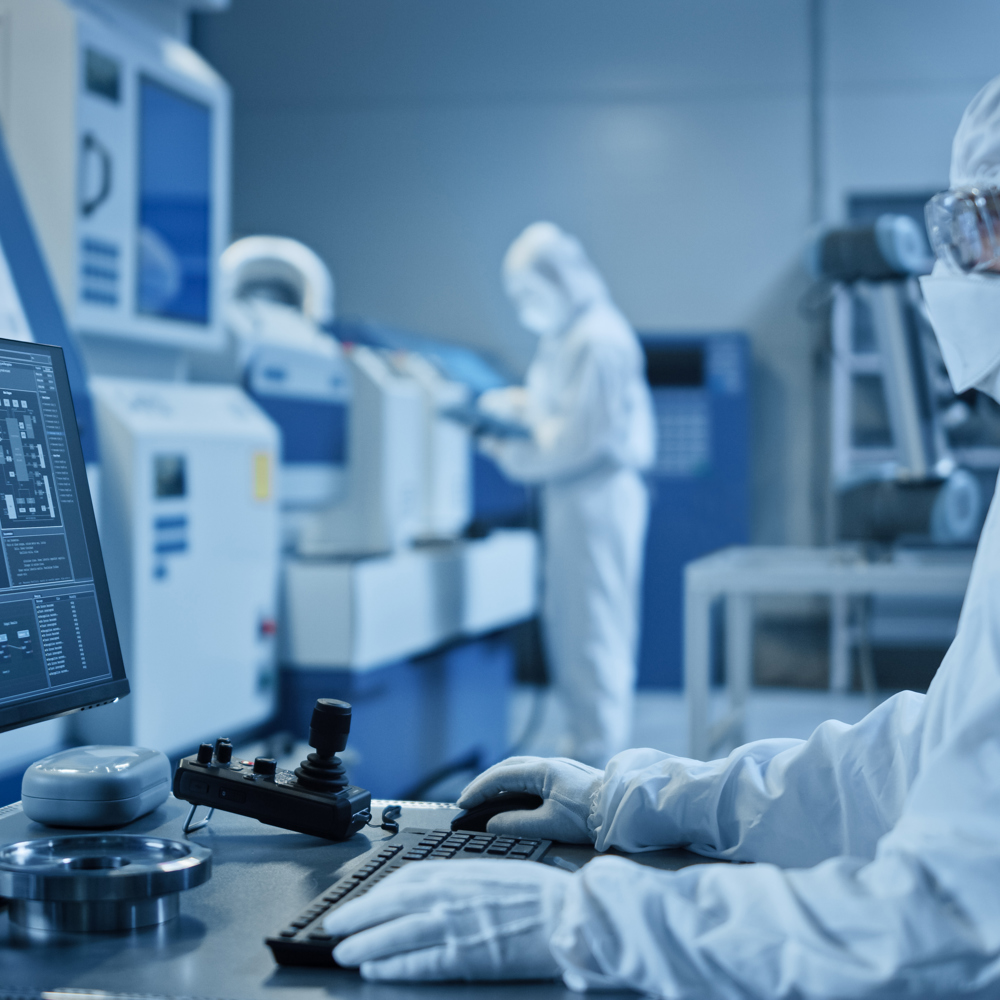
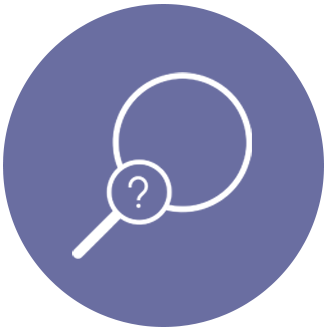
The Problem
When the COVID-19 pandemic started sweeping across the globe in late 2019 and early 2020, this company – a world leader in biotechnology research and innovation – sprang into action. With thousands of products in its portfolio, and a history of breakthroughs that have extended and improved the quality of patients’ lives, this company was in a strong position to lead the way in the development of a vaccine.
As early as February 2020, clinical trials were underway, and the company was making plans to scale production. At this point, several things were clear: Time was of the essence, and failure was not an option.
Developing the vaccine formulation was just the first hurdle in the race to deliver a COVID-19 vaccine to the public – and hopefully bring the pandemic to a swifter end. When the company began its engagement with RoviSys in summer 2020, the client already had commenced small-scale production at several of its facilities around the world.
As it prepared to ramp up production to meet regional and global demand, the company planned to repurpose existing manufacturing space at its Michigan facility, expanding the production area from 3,000 to 30,000 square feet for the COVID-19 vaccine. Working on an accelerated timeline, the goal was to design the production space and integrate brand-new processing equipment simultaneously. Because of the scope and fluid nature of the project, the company needed a partner with capabilities beyond those of a typical systems integrator.
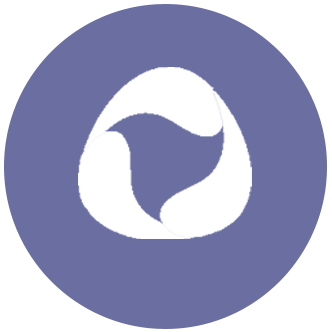
Our Role
Thanks to an established relationship with RoviSys, this client knew that RoviSys had the capabilities and proven experience to serve as a master systems integrator for this ambitious project. With the depth of talent to quickly mobilize dozens of qualified engineers, RoviSys could bring to bear more resources than a typical systems integrator. Ultimately, a team ranging from 25 to 40 RoviSys engineers contributed to the execution of this project over 18-month period.
As a Rockwell Automation Platinum System Integrator, RoviSys brought decades of collective experience designing and implementing complex automation systems in the life-science industry and a wealth of knowledge about Rockwell platforms. As a master integrator, RoviSys delivers tremendous value by not only the expertise of staff engineers, but also the ability to lead and manage subcontractors. Together, this unique mix of credentials and capabilities made RoviSys the logical choice to lead the integration effort.
The ultimate outcome of this project was a successful production ramp-up that resulted in the support of billions of doses of the vaccine globally.

The Solution
To support production of the vaccine, the company installed brand-new production equipment with proprietary capabilities such as lipid-nanoparticle (LNP) processing. The control platform included state-of-the-art Rockwell controllers, I/O cards, control panels, power panels and operator display stations. Leveraging deep expertise in application engineering, RoviSys designed and implemented the SCADA/HMI control system and batch code for the manufacturing and cleaning processes.
Rockwell’s distributed control system supports key functions such as LNP and filtration skid programming. The solution gives operators the visibility and real-time information needed for critical manufacturing decisions, providing capabilities such as 100% electronic batch reports and a fully automated clean-in-place (CIP). However, most of the production equipment came pre-programmed with standard onboard controls. To optimize the programming for the requirements of this project and assimilate the new controls into the plant’s production system, RoviSys leveraged its deep expertise in batch automation to integrate the new controls as part of a custom solution. One of the more complex tasks was designing and integrating the controls for the CIP system, which cleans the interior surfaces of valves, pipes, tanks and other process equipment. With a wealth of industry-specific experience and expert resources, RoviSys was able to design and implement a custom control architecture that meets the specialized requirements of pharmaceutical production – on an expedited timeline.
Overall, the project parameters were anything but typical. Just as the pandemic was a fluid situation in 2020, the scope of this project was in constant flux, and even the size of the production area wasn’t set in stone. Given the urgency of the situation, the strategy was to get the large systems in place first – so vaccine production could begin as soon as possible – and implement the smaller pieces as they became available. To accelerate the process, some steps that typically take place sequentially were executed simultaneously. The final qualifications included some adjustments to the cleaning cycles and overall process efficiency. Ultimately, RoviSys drove this project to the finish line by staying flexible and nimble, maintaining a collaborative and constructive relationship with the client and embracing a “can’t fail” mentality.
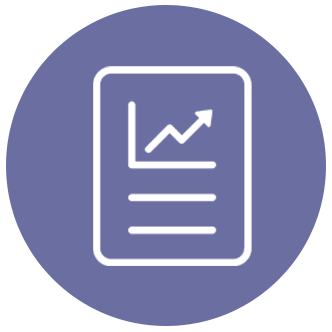
The Result
The accelerated development and production of a COVID-19 vaccine marked a turning point in the pandemic. By December 2020, the U.S. Food and Drug Administration (FDA) had issued an emergency-use authorization for the vaccine, and the FDA officially approved the vaccine in August 2021. Although no one is declaring an end to the pandemic, the unprecedented response by this biotech leader – with support from RoviSys – has played a critical role in protecting people around the world from the devastating effects of COVID-19.
The ultimate outcome of this project was a successful production ramp-up that resulted in the support of billions of doses of the vaccine globally. For the next phase of the project the team duplicated the original manufacturing facility while also continuing to enhance the automation supply around the batch process Incorporating additional system capabilities to support a new bi-valent vaccine product. The company has continued its partnership with RoviSys, thanks to the consistent leadership, support and automation expertise that RoviSys has provided over the course of multiple successful initiatives.