Driving Efficiency In Biotech Operations
To provide innovative technologies and solutions for its biotech customers, this skid manufacturer needed a modular process skid that would allow operations to quickly toggle between two key processes within the same system.
To meet the rapidly evolving needs of its biotechnology customers, a global provider of filtration, separation and purification systems knew it needed to look beyond industry norms for a solution that would give customers the operational flexibility and agility to adapt to ever-changing market conditions.
The company developed a modular skid that consolidates tangential flow filtration and chromatography into one unit, enabling operations to switch between two critical processes that previously required separate machines. To implement the control architecture for this industry-first product, the company needed a partner with deep expertise in process automation, systems integration and material management – and a proven history of success delivering game-changing solutions in the pharmaceutical industry.
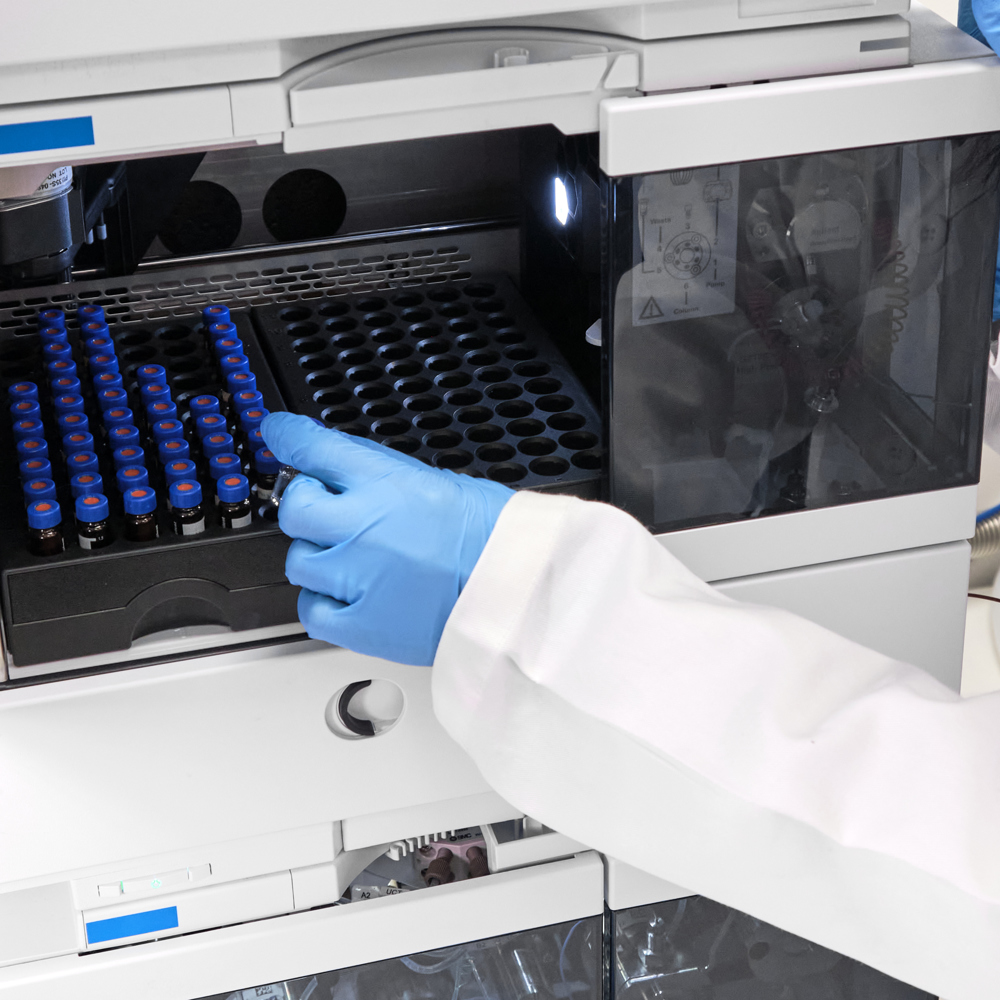
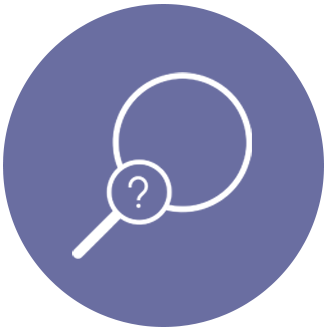
The Problem
In the quest to develop life-saving vaccines, medicines and treatments to address the world’s most pressing public health needs, biotechnology firms face a myriad of operational challenges – high R&D costs, long lead times and intense competition. The COVID-19 pandemic further underscores the critical importance of having multi-product manufacturing capabilities and flexible production systems that drive efficiencies and reduce lead times.
Driven by its mission to provide innovative technologies and solutions for its biotech customers, this U.S.-based skid manufacturer saw the need to develop a modular process skid that would allow operations to quickly toggle between two key processes within the same system: tangential flow filtration, a rapid and efficient method for separation and purification of biomolecules; and chromatography, a scientific process that has taken on added importance in the biotech field due to its ability to detect protein and other molecular matter.
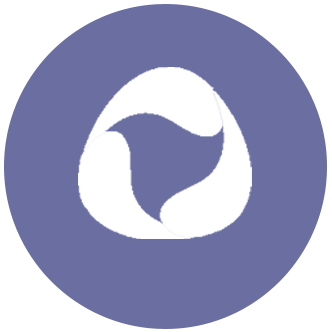
Our Role
With decades of collective experience implementing automation and information solutions for the pharmaceutical industry, RoviSys brought the industry-specific technical knowledge needed to execute this vision. Not only is RoviSys well-versed in the complexities of batch and process manufacturing, but RoviSys engineers also carry deep technical acumen in the utilization of S88 batch control to make processes as modular as possible.
This provider of filtration, separation and purification solutions had engaged RoviSys in the past, and knew that RoviSys had the resources, capacity and automation expertise to bring the project to fruition. RoviSys was uniquely qualified to maximize the capabilities of AVEVA software – the company’s platform of choice – in support of this project. As an AVEVA-endorsed systems integrator, RoviSys quickly identified that pairing the AVEVA System Platform with Batch Management would solve the challenges identified by this manufacturer.
Not only is RoviSys well-versed in the complexities of batch and process manufacturing, but RoviSys engineers also carry deep technical acumen in the utilization of S88 batch control to make processes as modular as possible.

The Solution
AVEVA Batch Management software excels in automating complex batch processes and managing flexible, multi-stream and multi product batch operations. To fully leverage this powerful software, RoviSys developed a batch control architecture adhering to S-88, the accepted standard for structuring automation projects.
The RoviSys team of engineers wrote S-88 compliant batch design, maximizing the capabilities of the AVEVA Batch Management software suite. Integration with AVEVA System Platform enabled the RoviSys team to design and configure dynamic Operator Interface Display switching. This design included custom properties, scripts, and animations to enable operations to toggle between tangential flow filtration and chromatography processes with the click of a button. Equipped with easy-to-use configuration tools, process engineers can quickly create or change recipe procedures and formulas – enabling them to deploy new recipes independently of automation support.
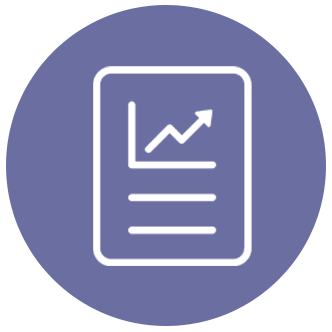
The Result
The custom-designed process skid is a game-changer for this manufacturer as well as other biotech and pharmaceutical companies. It streamlines previously disparate batch processes into one physical unit – all managed within an intuitive, robust and easy-to-use operating system that drives production efficiencies. The versatile skid makes it unnecessary to purchase bolt-on programs to increase production capabilities, and simplifies use of available plant capacity by simultaneously managing concurrent batch execution on networked equipment.
Leveraging AVEVA software suite, RoviSys designed a robust tracking and reporting platform that enables process engineers to easily create adhoc reports and detect out-of-spec performance. The reporting solution design by RoviSys delivers real-time data on production processes, equipment status and other key performance indicators (KPIs). Additionally, reports are generated automatically when batches are complete – directing batch activity, material flow and production data to a historical database for a full electronic batch record that complies with industry-accepted data retention policies.
RoviSys executed the project on schedule, and the skid manufacturer is planning additional skid solution design and feature enhancements to their existing skid systems. With RoviSys as a strategic partner, the timetable for replicating this process – from initial design to commissioning – has been reduced from months to weeks. Leveraging the strengths of the AVEVA System platform templates has enabled this skid vendor to reduce the effort of future skid deployments – which has resulted in a savings of nearly 75% on engineering effort.