Design-Assist Seals The Deal: A Smart Partnership In Specialty Chemicals
In order to meet COVID-fueled demand for its coatings and sealants, the company needed to build a new production facility, and capitalize on an unprecedented interest in home-renovation projects.
The construction and home-improvement market has been growing steadily over the past decade, and the COVID-19 pandemic pushed demand to record levels. This U.S.- based manufacturer of specialty building materials is well-positioned to capitalize on the unprecedented interest in home and commercial improvement projects. But, in order to meet surging demand for its coatings and sealants, the company needed to build a new production facility… something it hadn’t done in over 25 years.
With 90,000 square feet of manufacturing space – including eight fully automated production lines – the new facility would provide the capability to simultaneously mix eight different products and then package them for shipment. Ultimately, this Greenfield facility would enable the company to quadruple its capacity for production of sealants and waterproofing products.
The project also presented a golden opportunity to harness cutting-edge building control and process control systems, and incorporate the latest automation technology. Today’s automation platforms provide a comprehensive picture of production processes and equipment performance, and they’re integrated with facility controls and power management tools that provide insights to improve operational and financial results.
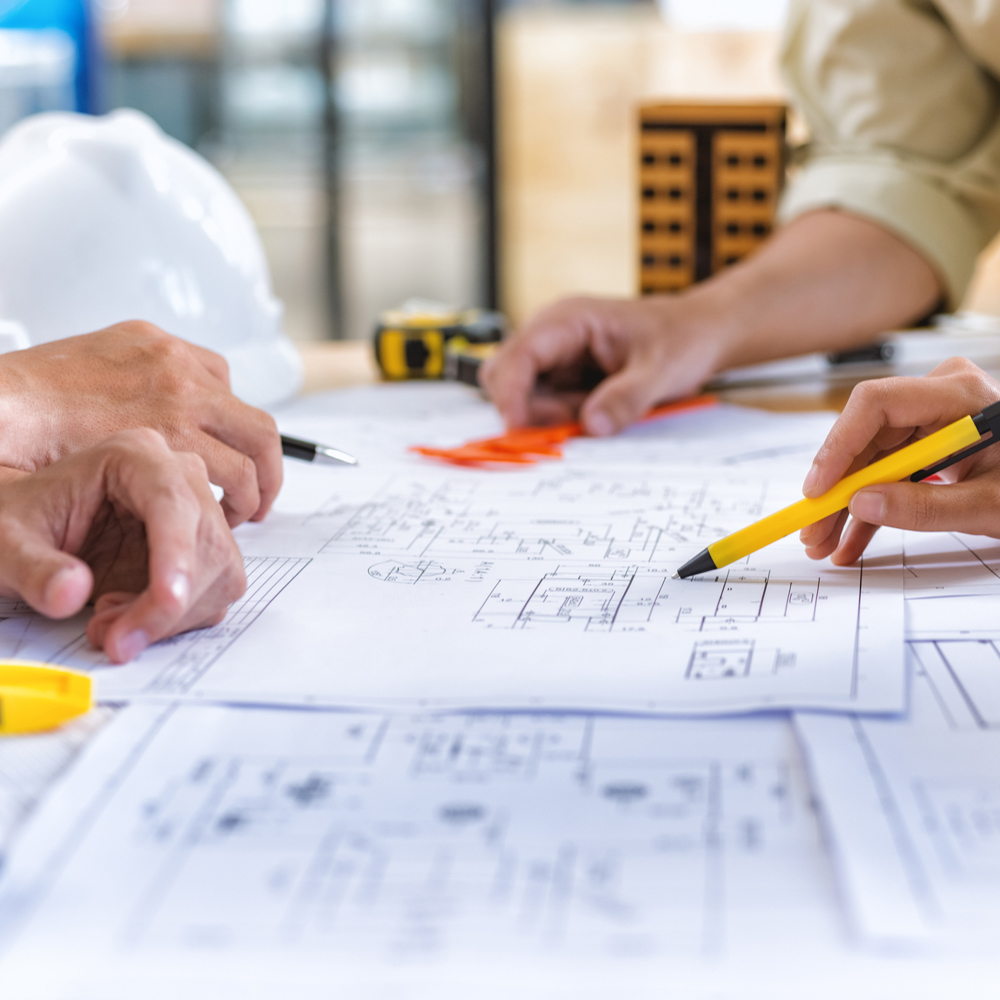
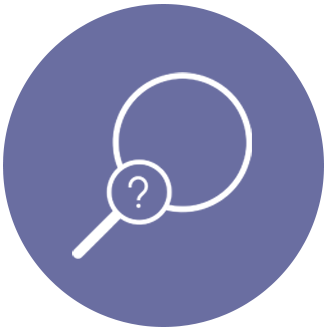
The Problem
The company had worked with RoviSys on small projects in the past, but this was a larger scope than anything they’d tackled together. With this endeavor, they were starting from scratch. The existing plant wasn’t custom-built for the company, and there was no process-framework documentation to use as a baseline for the new facility.
Adding to the complexity of the project was the vast array of control and automation technologies available on the market. The customer had a team of process engineers, but not a dedicated facility management team familiar with integrating facility support systems. Without that, the process of specifying and sourcing the right mix of automation technology solutions for the new facility would have been overwhelming and inefficient.
The company’s needs far exceeded the capabilities of a typical systems integrator (SI). For this $25 million Greenfield project, the customer required a consultative partner with deep expertise in both process automation and building automation – not to mention decades of boots-on-the-ground experience in the specialty chemicals industry.
This customer needed a Process Automation Partner and Master Systems Integrator (MSI) that would drive the design, selection and implementation of control systems utilizing the best connected technologies to optimize productivity, safety and efficiency.
With decades of collective experience delivering custom process and building automation services and solutions for batch manufacturers, RoviSys had the depth of expertise and resources to deliver the results this customer required in the near-term, and offering plenty of flexibility to pivot and grow based on future market demands.
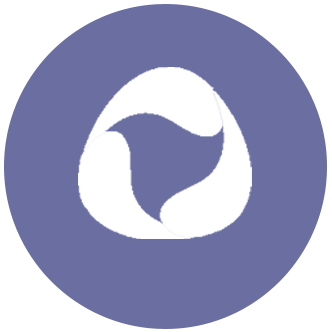
Our Role
RoviSys engaged with this customer in the very early stages of the project. In the discovery phase, the RoviSys team spent four months conducting a comprehensive analysis of the customer’s existing systems and processes, gathering information about the building layout and infrastructure requirements, and getting a clear understanding of the company’s operational needs and objectives. This collaborative process built trust with the customer, and enabled RoviSys to make customized recommendations detailing the framework and technology for this new facility.
Built on a true partnership approach to system design and integration, RoviSys provided a holistic solution that included consulting services, network infrastructure and security, electrical design and control systems – eliminating the need for the client to manage multiple contractors. RoviSys made specific recommendations for the integration and location of automation equipment, and provided guidance on connecting the information technology (IT) and operational technology (OT) infrastructure to ensure seamless interaction between business and manufacturing systems.
It was an effort that required collaboration with IT personnel, production teams, plant managers and operators. As an MSI with a long track record of proven project management, RoviSys was ideally suited to synthesize all of the input from these stakeholders into a comprehensive, cohesive automation strategy.
Ultimately, this was a collaborative effort between the client and the RoviSys Building and Process Automation groups. A team of eight RoviSys engineers collectively logged approximately 6,000 man-hours on this project, while a dedicated project manager streamlined planning and communication, providing a single point of contact for the client team.
The ultimate deliverable is a truly connected, smart production facility with fully integrated automation – a 21st-century solution for the complexities of modern manufacturing.

The Solution
RoviSys built a cross-functional project team with a combination of Process Automation and Building Automation groups. The team mapped out the control architecture for the manufacturing operations and building systems, including: HVAC, fire alarm monitoring, power quality, facility support systems, formulation/recipe management, dosing, mixing, packaging, inline quality checks, raw material tracking and reporting, and operating efficiency reporting. As a vendor-independent organization,
RoviSys was able to determine solutions that were right for this customer from a broad range of technologies and vendors based on their specific requirements. In this case, the customer uses Rockwell Automation solutions in its existing facilities. To deliver a unified technology approach, RoviSys recommended Rockwell Automation products for the new facility,
including:
- FactoryTalk Batch
- FactoryTalk Historian
- FactoryTalk View
These solutions are designed to provide a comprehensive picture of production operations across entire lines and processes – providing the insight and tools to increase equipment utilization, improve product quality, reduce costs and leverage operational data for greater productivity and efficiency.
The key to maximizing the potential of these solutions is having a partner with the expertise and resources to integrate them into a cohesive, seamless automation strategy. And that’s where RoviSys shines.
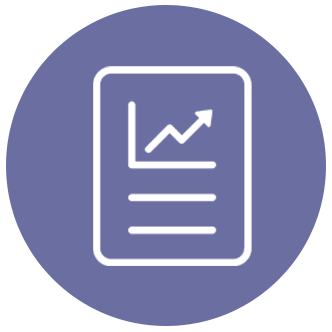
The Result
This customer began the journey of building and automating an entirely new facility with plans and challenges that needed to be addressed upfront and throughout the project. As with any project of this magnitude, adhering to timelines, budgets and organizational planning are key to success.
RoviSys was able to deliver all aspects of this project on time and on budget, enabling the customer to begin operating in a smart, secure facility that leverages reliable, best-in-class technologies to transmit the right data to the right people in an accessible, actionable way. With more control and visibility of its manufacturing data and equipment, the company has boosted production and has seen a steady uptick in business.
With these cutting-edge automation and control systems in place, operators have a “single-pane-of glass” view into the status of nearly every operating and building system within the facility, easily accessible on tablets and smartphones. The ultimate deliverable is a truly connected, smart production facility with fully integrated automation – a 21st-century solution for the complexities of modern manufacturing.
Based on the success of this project, the customer has engaged RoviSys to provide consulting and engineering services for other facilities around the world.