Custom Solution To High Volume Challenges
From dashboards to machine learning: In order to improve quality, throughput, and availability in its high-volume facility, this distribution center required a custom solution that could efficiently move and track material through its ever-shifting logistical puzzle.
With millions of units moving through its global warehouse network, this fulfillment giant faced a complex challenge to both efficiently move each product in its vast inventory and to accurately track that movement through the facility. Success in both of these challenges is essential to achieve the throughput metrics and real-time availability data the business—and its customers—demand.
Doing so, however, requires the careful integration of multiple systems and data sources to fuel a complex master tracking system that can coordinate and track each piece of this logistical puzzle, while also identifying issues and bottlenecks to improve productivity.
For this company, the answer came in a custom solution to expose and aggregate data from the shop floor level into SCADA and business intelligence systems systems that could leverage machine learning techniques to identify bottlenecks and suggest improvements.
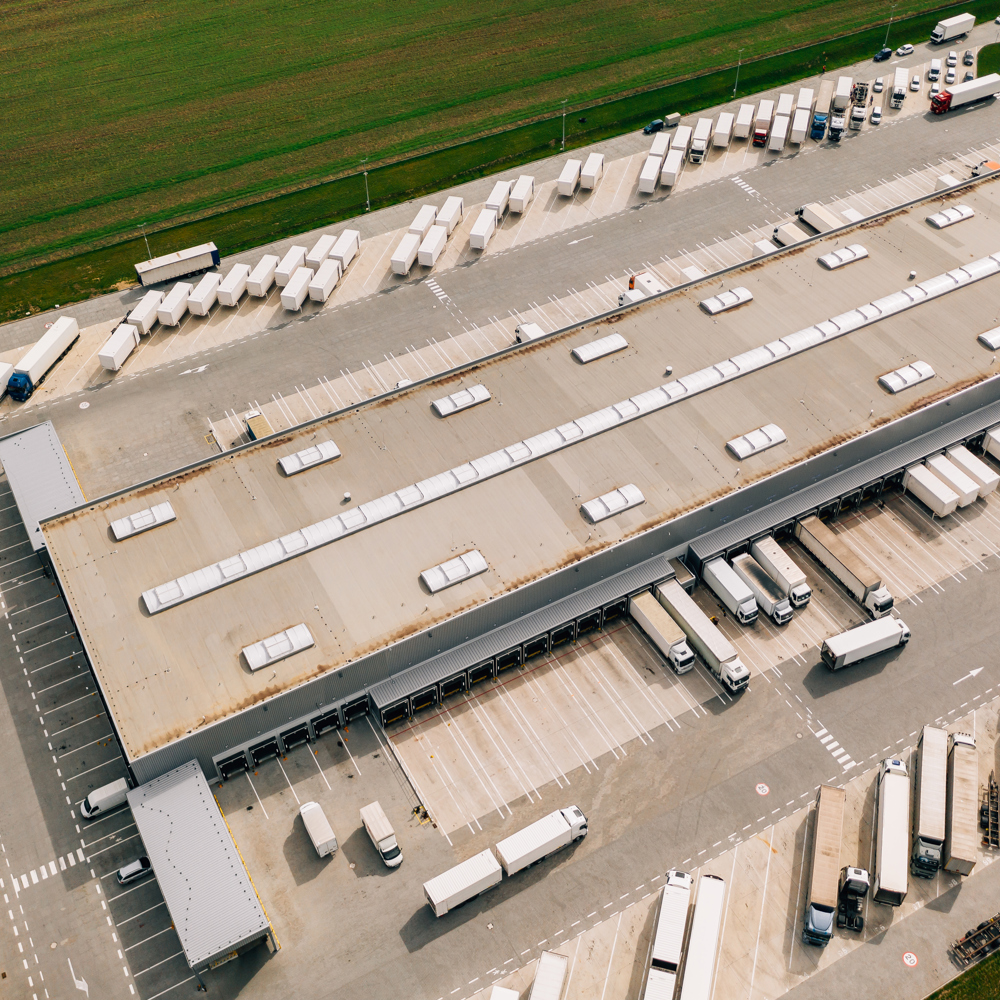
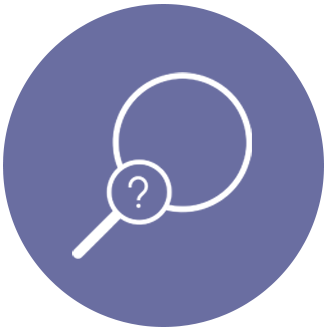
The Problem
Successfully managing the product flow through such a massive, complex warehousing and distribution network requires deep insight and actionable intelligence that penetrates every process and movement within the facility. However, this organization was operating without that insight, tracking its product movements without the aid of analytics, dashboards, or other modern tools used to keep complex operations running smoothly and cost effectively.
As a result, factors that may have been significantly impacting warehouse performance, from bottlenecks to labor distribution to root causes were being missed.
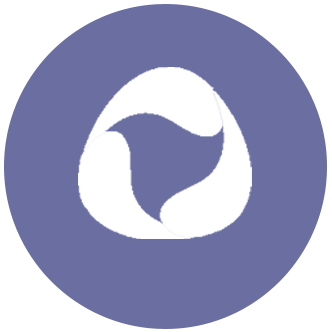
Our Role
Given the sheer volume of products handled in these distribution centers and the complex trail of data it carries, this customer required a partner with expertise far beyond that of a typical integrator. Success in this endeavor was determined by the ability to coordinate data streams from eight different interfaces and logic controllers produced by eight different vendors into a custom-built system unlike any off-the-shelf product available in the world today.
For this monumental task, RoviSys carries the experience and deep technical expertise required to produce the intended results. Built on a holistic, vendor-independent approach to system design and integration, RoviSys integrated high volume data feeds into a coherent, effective system that marries established technologies and cutting-edge innovations to ensure success even in this demanding environment.
Thanks to this coding and the strong results from the initial implementation, this solution has already been deployed to more than 50 warehouses worldwide.

The Solution
The primary objective in this project was to develop a system that could seamlessly integrate data streams from multiple disparate sources used across the distribution and warehouse facilities: Ignition SCADA, Cognex DataMan, ASInterface, SEW MOVI Drives, PowerFlex Drives, ControlLogix PLC, Siemens S7 PLC, and others.
To do this, RoviSys developed a custom solution stack based on Inductive Automation’s Ignition platform. This system pulls together all the required data from the various subsystems to track quality, throughput, and availability of products throughout warehouses. RoviSys also provided detailed, user friendly dashboards and reports designed to classify warehouse performance, identify faults, and direct labor more efficiently
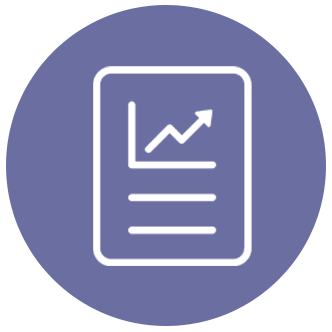
The Result
The fundamental problem for this customer was the lack of analytics-driven insight into its operations. With this new system, built from Ignition software and machine learning technologies, the customer can now rapidly identify bottlenecks and efficiency problems across the busy warehouse and tie them back directly to root causes. With that insight, the company can accelerate its operational strategy, maximizing quality, throughput, and availability.
The impact of the solution extends far beyond the challenges of this particular warehouse and distribution center. The improvement opportunities it provided were deigned to be scalable and robust enough to roll out across the entire enterprise, requiring only site-specific data to be mapped into the standard libraries as it expands. Thanks to this coding and the strong results from the initial implementation, this solution has already been deployed to more than 50 warehouses worldwide.