Automaker Turns to RoviSys for Facility Retrofits
This U.S. automaker was paying a steep price for out-of-date HVAC and building control systems in its legacy facilities – and the maintenance contracts that came with them. To control costs and boost operator comfort and safety, a technology refresh was needed.
This Big Three automaker has modernized its domestic manufacturing plants with cutting-edge robotics
technology and optimized its facilities for efficient flow of materials and processes. However, the
decades-old building and climate control systems have been a drag on costs, energy efficiency and
operator comfort.
The automaker needed to update these building systems without interrupting production – a challenge
that required the expertise and experience of a trusted master systems integrator.
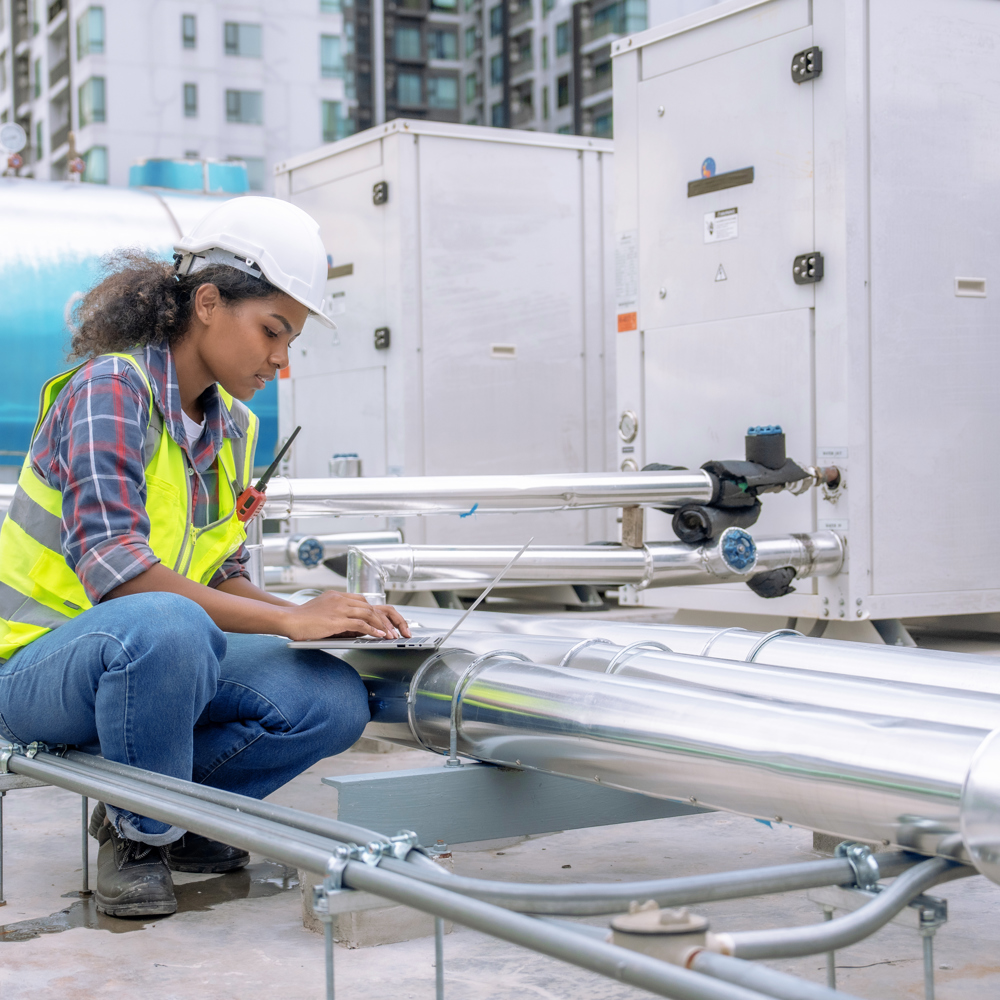
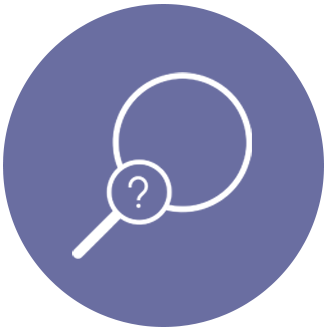
The Problem
Two U.S. assembly plants – each of which opened in the early 1950s – relied on building systems that were more than 20 years old. The facilities’ HVAC infrastructure includes ductless twin-blower air-handling units and direct-fire burners, which were by a design-engineering firm in the late 1990s as part of an energy-efficiency contract encompassing 12 of the automaker’s North American facilities. At the time, the project was a big step forward for a company striving to be greener, eliminating steam boilers and antiquated HVAC units. The project had included installation of Bigfoot heating and ventilation systems, which are designed to maintain uniform building temperature and positive pressure without ductwork. The Bigfoot systems modulate airflow using VFD blowers and damper control.
Retrofitting the facilities with newer technologies in the late 1990s helped improve energy consumption and greenhouse-gas emissions. However, these systems lacked robust automated controls as well as detailed schematics. As time went on, the systems became unreliable, requiring additional man-hours for correcting issues and providing support. By the time the client engaged RoviSys, the computer controls were over a decade old and were reaching the end of their service life. The hardware and software had become obsolete, which increased the likelihood of system failures and process interruptions – leading to overrides and inefficient use of energy. In addition, the automaker was locked into a multimillion-dollar annual service contract, which prevented them from utilizing more cost-effective solutions.
With the expiration of the contract, the automaker had an opportunity for significant change. The computer controls were in dire need of software and hardware updates to maintain their documented efficiencies. There was a clear need to refresh the legacy building systems – and to find a more cost- effective alternative to the annual maintenance contracts. However, implementing a solution would not be easy. The two facilities assemble some of the company’s most popular models, and production couldn’t miss a beat. It’s been estimated that a single minute of unplanned downtime costs the average automaker a whopping $22,000. The project would need to be executed quickly and flawlessly, accommodating production schedules, seasonal temperatures and other constraints.
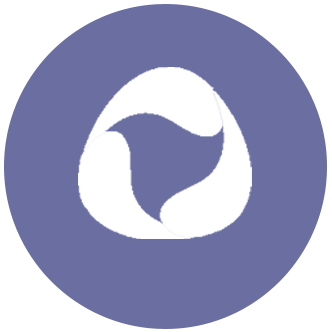
Our Role
The RoviSys Building Technologies (RBT) was the clear choice to execute this project. RBT’s capabilities extend far beyond those of a building controls specialist or system integrator. RoviSys is a master systems integrator with a proven history of partnering with automotive manufacturers in the design,
engineering, implementation, installation and commissioning of building management and building automation systems.
RoviSys has the resources, capabilities and industry-specific experience to develop innovative solutions for the most complex operational challenges in automotive facilities – a true partner that can deliver full-scale integrated control platforms while working within the parameters of clients’ core operations.
Prior to this project, RBT had partnered with the automaker on a refurbishment/BMS initiative at another North American facility that included paint shop and office space improvements. By delivering a successful outcome there, RoviSys set the stage for additional opportunities with this client. Plus, RBT’s physical proximity to the automaker’s U.S. facilities added to the client’s comfort level. Ultimately, the client’s decision to continue its engagement with RoviSys was an easy one.
RoviSys has the resources, capabilities and industry-specific experience to develop innovative solutions for the most complex operational challenges in automotive facilities – a true partner that can deliver full-scale integrated control platforms while working within the parameters of clients’ core operations.

The Solution
RoviSys Building Technologies did the technical “heavy lifting” for this project. Deliverables included controls engineering, onsite commissioning and full BMS integration. The RBT team selected the Tridium Niagara 4 platform as the central console for the revamped control architecture. Other significant technology improvements included built-in OPC support and connectivity, TCP/IP networking and mitigation of hardware/software obsolescence issues. RBT also coordinated the various subcontractors, providing a single point of contact for the client.
In the assessment phase, RBT visited each site to conduct a detailed analysis of the existing building systems and control architecture. A key element of the overall project plan was the front-end engineering design (FEED) study, which defined the project scope and included the technical documentation and procedures needed to keep the systems running.
The refurbishment project was a complex undertaking, involving retrofitting, re-engineering and replacing controls and instrumentation, and configuring the network infrastructure.
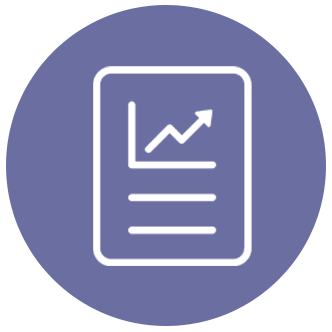
The Result
The refurbishment initiative has breathed new life into the HVAC systems. One of the most significant upgrades is the improved graphical interface, which provides real-time visibility into the status and condition of building equipment, enabling operators to optimize HVAC performance and efficiency. The easy-to-use interface helps to reduce troubleshooting times, and it reduces the amount of training required to operate equipment. Operators can easily view detailed spreadsheets or graphs that compare daily and monthly gas and electric usage to the projected usage, promoting better energy management.
As part of the project, RBT trained onsite personnel to maintain the building and control systems. Consequently, the facilities no longer rely on service contracts to keep these systems running – a huge annual cost savings.
Overall, RBT delivered the expected results for this project, on time and under budget. And because RoviSys has demonstrated the ability to consistently deliver solutions that support refurbishment initiatives across the automaker’s North American footprint – without incurring any unscheduled downtime – there’s an efficient, repeatable process for future projects.