Accelerating The Next Revolution In Medicine
To bridge the gap between research and commercialization of cell-based therapies, a leading university teamed up with this global solutions provider to build and operate a state-of-the-art innovation center. Thanks to its proven experience supporting life-sciences manufacturing, RoviSys Building Technologies (RBT) played a key role in the project execution.
Cell-based therapies hold the promise of breakthrough treatments for a variety of diseases and conditions. As a global leader in solutions that drive innovation and productivity in the sciences, this RoviSys client is well positioned to help research organizations implement standardized approaches that shorten development timelines, drive down costs and avoid pitfalls on the path toward commercialization.
This company was a logical choice to build and operate a 44,000-square-foot R&D, manufacturing and collaboration center dedicated to accelerating the commercialization of life saving cell therapies, in strategic partnership with a leading public research university. Pairing the university’s leadership in cellular immunotherapy with the company’s extensive capabilities in cell therapy instrumentation and manufacturing, the partnership could be a game changer for patient care.
To implement and integrate the sophisticated building automation systems needed for a precisely controlled environment, RoviSys Building Technologies was the logical choice as well.
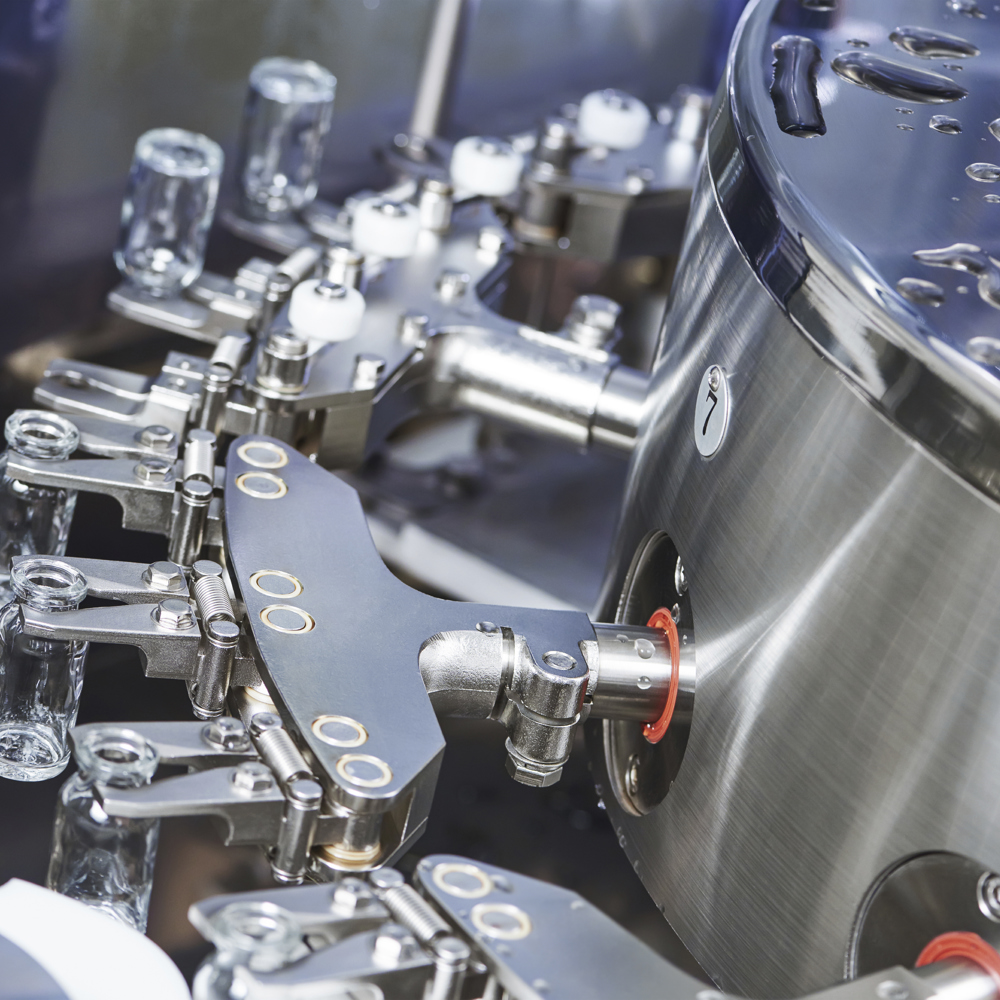
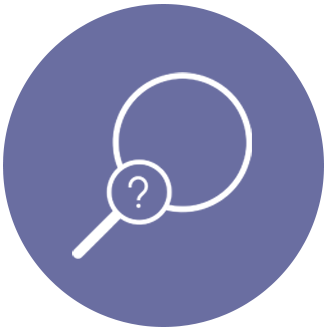
The Problem
The innovation center will offer clinical and commercial cell-therapy manufacturing services, in line with Current Good Manufacturing Practice (CGMP) regulations, and it will serve as a hub for manufacturers and researchers to leverage the client’s broad portfolio of cell-therapy systems and technologies. It’s an ambitious undertaking with the potential to significantly advance research methods, accelerate the production of commercially available therapies, and improve patient access to transformative treatments.
For this complex project, the company needed a building automation partner with the wherewithal to retrofit an entire facility – including HVAC systems – and a proven history of implementing facility automation solutions for highly controlled environments. The client also needed a partner that’s well-versed in Rockwell Automation platforms for process automation and building automation.
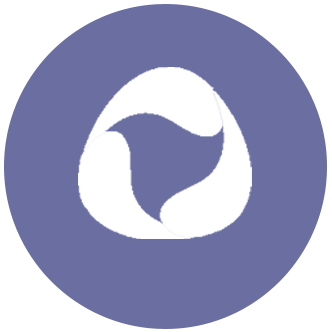
Our Role
After submitting an RFP in conjunction with a general contractor, RoviSys Building Technologies emerged as the clear choice to deliver exactly what the project needed. An established relationship with the healthcare company and its global subsidiaries, paired with decades of experience designing, building, installing and maintaining automation solutions for facilities with labs, clean rooms and other critical environments.
The customer was utilizing the Allen-Bradley/Rockwell Automation control system for its process automation, and preferred this same technology for its building automation. As a Rockwell Automation Platinum System Integrator, RoviSys was in an ideal position to specify, design and implement an integrated control platform that not only would meet the customer’s needs but also would be familiar to facility operators – so the customer could hit the ground running when the facility was ready.
The customer is confident that it chose the right partner - RoviSys Building Technologies - for this groundbreaking project.

The Solution
A dedicated team of engineers shepherded this project from planning, design and procurement to factory acceptance testing and commissioning, in about a year. Throughout the design and engineering process, RoviSys Building Technologies maintained a collaborative relationship with the client, functioning as an owner’s rep by keeping the customer’s best interests in mind at all times.
The scope of the project included integration of air-handling units, make-up air units, condensers, chillers, boilers, pumps and modular cleanrooms into the new environmental controls system. With more than 100 data-acquisition devices integrated into the new control infrastructure, the facility will be able to leverage operational data to help improve equipment efficiency, minimize energy consumption and intervene quickly when problems arise.
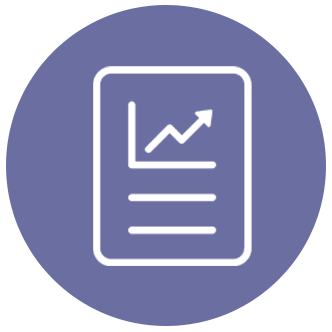
The Result
A single, integrated facility-wide control architecture provides a unified platform for process automation, environmental monitoring and building management. With a unified approach, the same functionality applied to process control validation is used to meet validation requirements for building automation.
The control architecture is the foundation for a stable operating environment that meets FDA requirements and requirements established by the customer. Rockwell Automation system architectures are TÜV-certified to the international standard ISA-99/IEC 62443-3-3, providing peace of mind that the system meets the industry’s stringent cybersecurity standards.
With full BMS integration, authorized personnel have the real time visibility to ensure that equipment is running at peak energy efficiency. Facility managers, engineers and operators receive email and text notifications on their mobile devices when equipment or environmental conditions generate critical alarms, and they can stay ahead of trends and potential problems by easily connecting live and historical data into reporting and analytics tools.
Because the customer’s personnel were familiar with Rockwell Automation systems for process automation, the learning curve with the new BMS has been a short one. Development of potentially life-saving cell therapies is underway, and the customer is confident in its understanding of the automation technology and confident that it chose the right partner for this groundbreaking project.